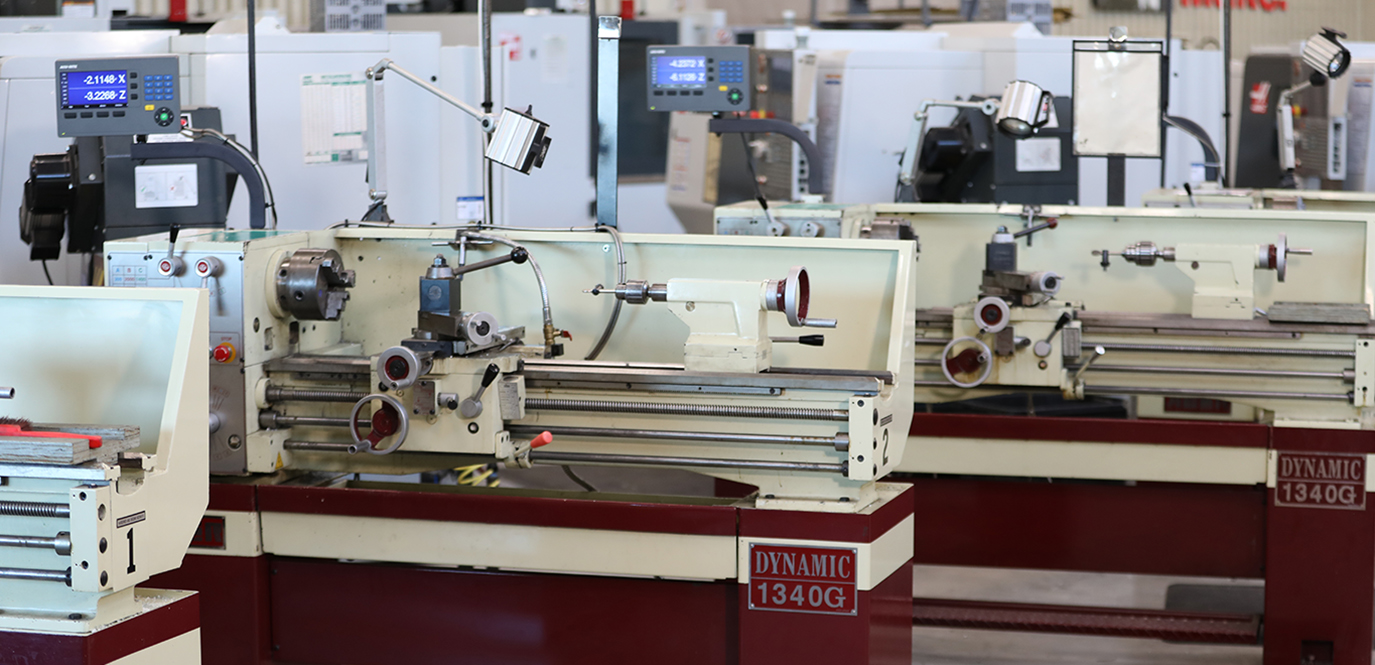
Ongoing advancements in precision machining are reshaping manufacturing processes. Manufacturers that embrace these technologies can rapidly accelerate their machining efficiency and capability. In 2025, we expect to see five key trends fueling adoption and investment in precision machining technology. Keep reading to explore them and discover how Acu-Rite Solutions is at the forefront, driving innovation to support the future of manufacturing.
Trend #1: Bluetooth® Integration
Bluetooth® adoption in manufacturing is on the rise. Analysts at ABI Research anticipate that global annual shipments of Bluetooth®-enabled industrial devices will grow six-fold between 2022 and 2028. According to ABI Research, Bluetooth® technology is increasingly essential in industrial digitization because of its energy efficiency and low cost.
Bluetooth® technology enables greater accuracy and efficiency in machining by transferring real-time measurements and data between machine tools and mobile devices. For example, the Acu-Rite Solutions droPWR iOS app integrates Bluetooth® technology and an IBT interface box to turn an iPad® into a digital readout.
With the first-of-its-kind droPWR application, an iPad® can do everything an Acu-Rite Solutions digital readout can do except without cables between the tablet and machine tool. It can connect to multiple machine configurations in one tablet, including for milling, turning, and grinding machines with up to six axes.
Since droPWR launched in 2022, downloads have increased annually, signaling greater adoption of Bluetooth®-enabled devices in machining workflows. The droPWR iOS app exemplifies how Bluetooth® powers more precise, flexible, and efficient machining.
Tour the droPWR Application-based Digital Readout
Trend #2: Reshoring
Reshoring became a strategic priority for many manufacturers amid the COVID-19 pandemic, which caused remarkable disruptions in the global supply chain. The recent announcement of potential shifts in U.S. trade policy has manufacturers bracing for more supply chain shifts.
In 2025, manufacturers who purchase from suppliers outside the U.S. may have to pay more for the materials and technologies that fuel their production. Those that prioritize domestic suppliers will be in good company. According to recent research by Bain & Company, 81% of CEOs and COOs reported plans to bring their company’s supply chains closer to home, an increase of 18% since 2022.
Manufacturers can reduce supply chain risks by purchasing digital readouts and CNC controls from domestic suppliers, such as Acu-Rite Solutions. We are proud to have designed, built, and supported our technologies from America since day one.
Sourcing precision machining technologies domestically in 2025 can help manufacturers control costs and secure faster lead times, support, and service. Reshoring will unlock greater operational efficiency for many.

Trend #3: Sustainability
U.S. environmental regulations are becoming stricter, which will make sustainability a business goal for many manufacturers in 2025. Some imminent regulations include rules by the Securities and Exchange Commission (SEC) requiring public companies to report on their environmental impact and more rigorous state requirements for emissions and renewable energy.
We can expect to see companies upping their investment in sustainability efforts to address these new regulations. Only 1% of the 300 public and private companies surveyed in early 2024 by Morgan Stanley said that sustainability is not significant to long-term corporate strategy.
Among manufacturers, there are other reasons behind the growing investment in sustainability:
- Aligning with corporate values
- Creating a cleaner and healthier environment
- Improving company reputation
Automation will continue to be an effective strategy for reducing the environmental impact of manufacturing. For example, precision machining technologies reduce material waste caused by errors and defects through greater accuracy and consistency. Less time spent on rework can lower energy consumption.
Precision machining contributes to a more efficient manufacturing environment, making it a critical enabler of sustainable manufacturing practices.
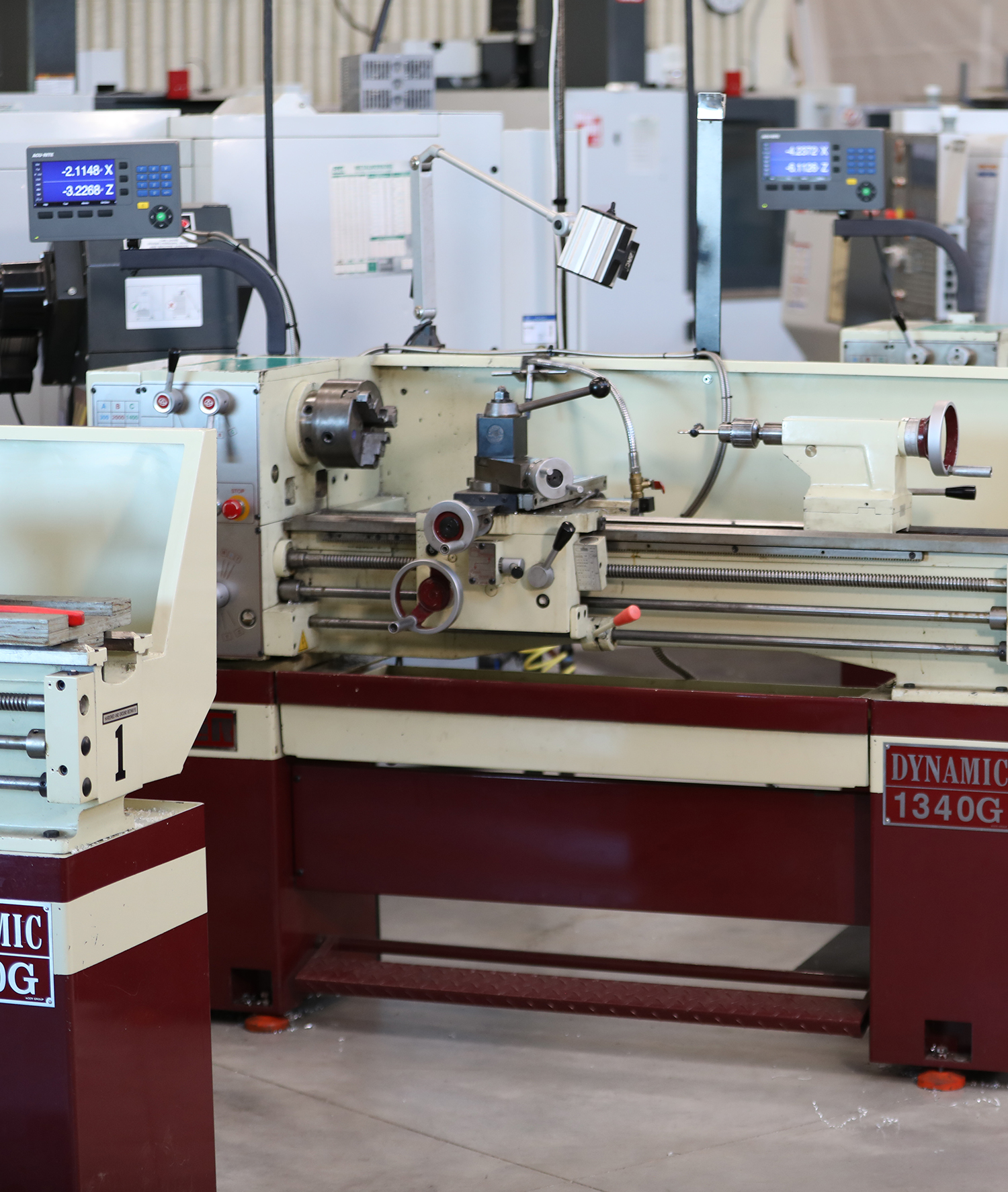
Trend #4: Precision Machining Technologies in Schools
In early 2024, a Manufacturing Institute and Deloitte report revealed that the U.S. manufacturing industry could require 3.8 million jobs to be filled in the next 10 years. Fortunately, enrollment in related education programs is rising. As a result, we could see colleges, universities, and trade schools invest in and upgrade their precision machining technologies to support real-world learning.
Here are a few indicators of the resurgence in manufacturing-related education:
- Engineering Enrollment: In the 2023-24 school year, undergraduate enrollment in engineering majors at four-year institutions increased by 6.1%, marking the first increase in five years.
- Skilled Trade School Enrollment: Enrollment in skilled trade schools was declining at 4.2% CAGR before the COVID-19 pandemic but grew at 1.2% CAGR from 2020 to 2023.
- Manufacturing Degrees: The number of associate’s degrees conferred between 2011-12 and 2021-22 rose by about 11% in the manufacturing, construction, repair, and transportation fields.
Precision machining technologies help educators prepare students for practical manufacturing, engineering, and machining challenges. Students at the Southern Illinois University College of Engineering use Acu-Rite Solutions digital readouts to design and produce parts. Horry-Georgetown Technical College teaches students foundational to advanced machining skills with Acu-Rite Solutions technologies in its machine tool lab.
Institutions that invest in cutting-edge precision machining technologies equip students with the skills and experience to thrive in the ever-evolving manufacturing industry.
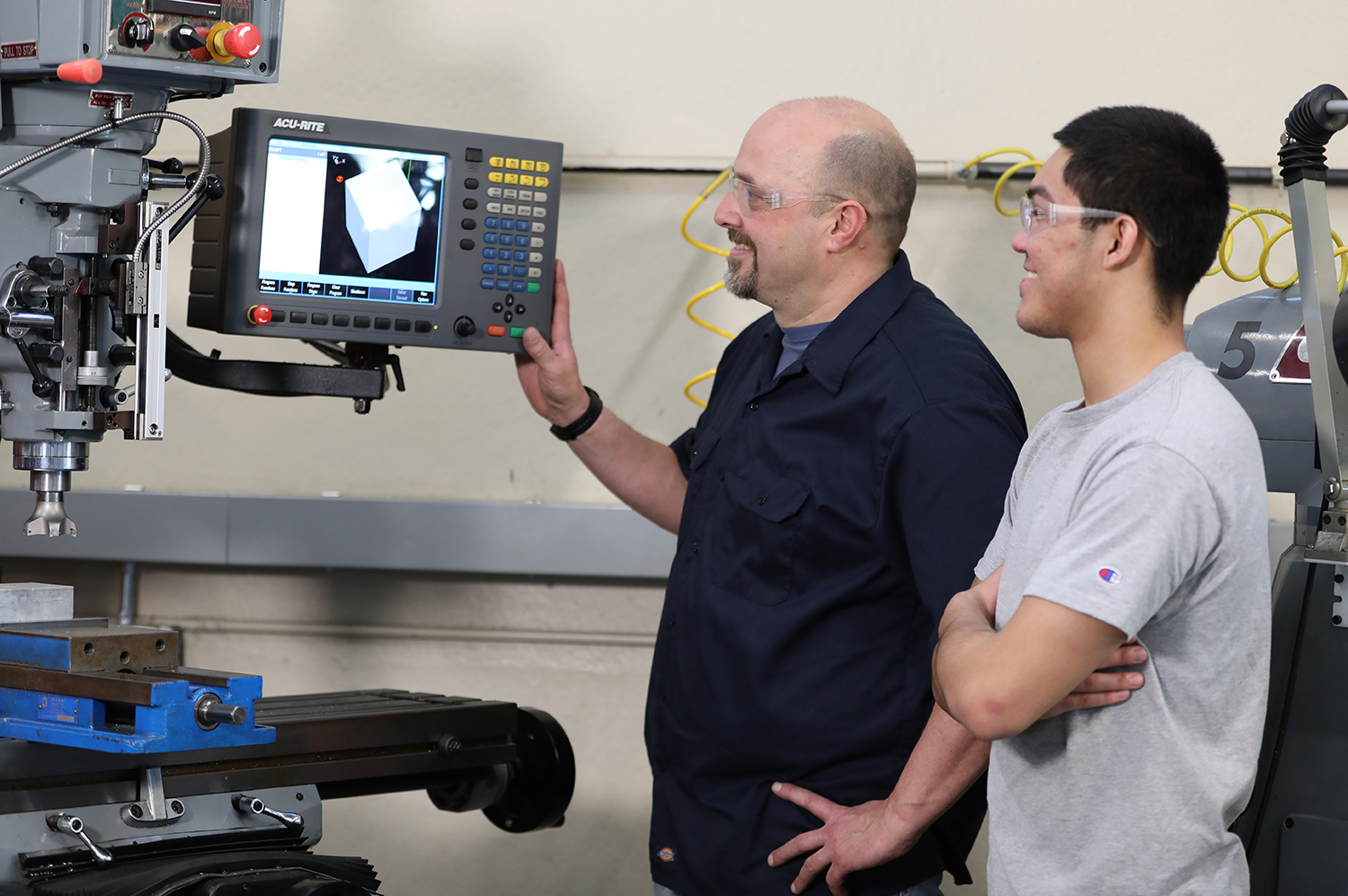
Trend #5: Improved User Experience (UX)
The UX of digital readout and CNC control systems has significantly improved thanks to ongoing technological advancement. In 2025 and beyond, we can expect further innovation to support the current and future manufacturing workforce.
Half of all U.S. manufacturing workers are age 44 and over. This median age indicates that much of the workforce is nearing retirement while fewer younger workers are entering the field. UX improvements will make precision machining technologies more user-friendly for machinists of all experience levels while attracting the next generation of workers.
We think these UX features, which improve the speed and accuracy of machining operations, will eventually become standard:
- Intuitive Interfaces: User interfaces (UI) will become more intuitive with simplified workflows, customizable settings, and touchscreen displays, allowing machinists to adapt to new technologies quickly.
- Ergonomics: Precision machining technologies will be designed with adjustable screens, ergonomic keyboards, and other features to minimize operator strain.
Acu-Rite Solutions has long been at the forefront of UX advancements because our technologies are designed for machinists from entry-level to experienced. Backed by the continuous innovation of HEIDENHAIN, we are dedicated to continually advancing ease of use and accuracy. Our digital readouts and CNC controls feature graphical and text-based displays, touchscreens, customizable display layouts, automatic error detection, ergonomic keyboards, and more.
In 2025, we are excited to continue leading the endless pursuit of greater machining accuracy and efficiency.
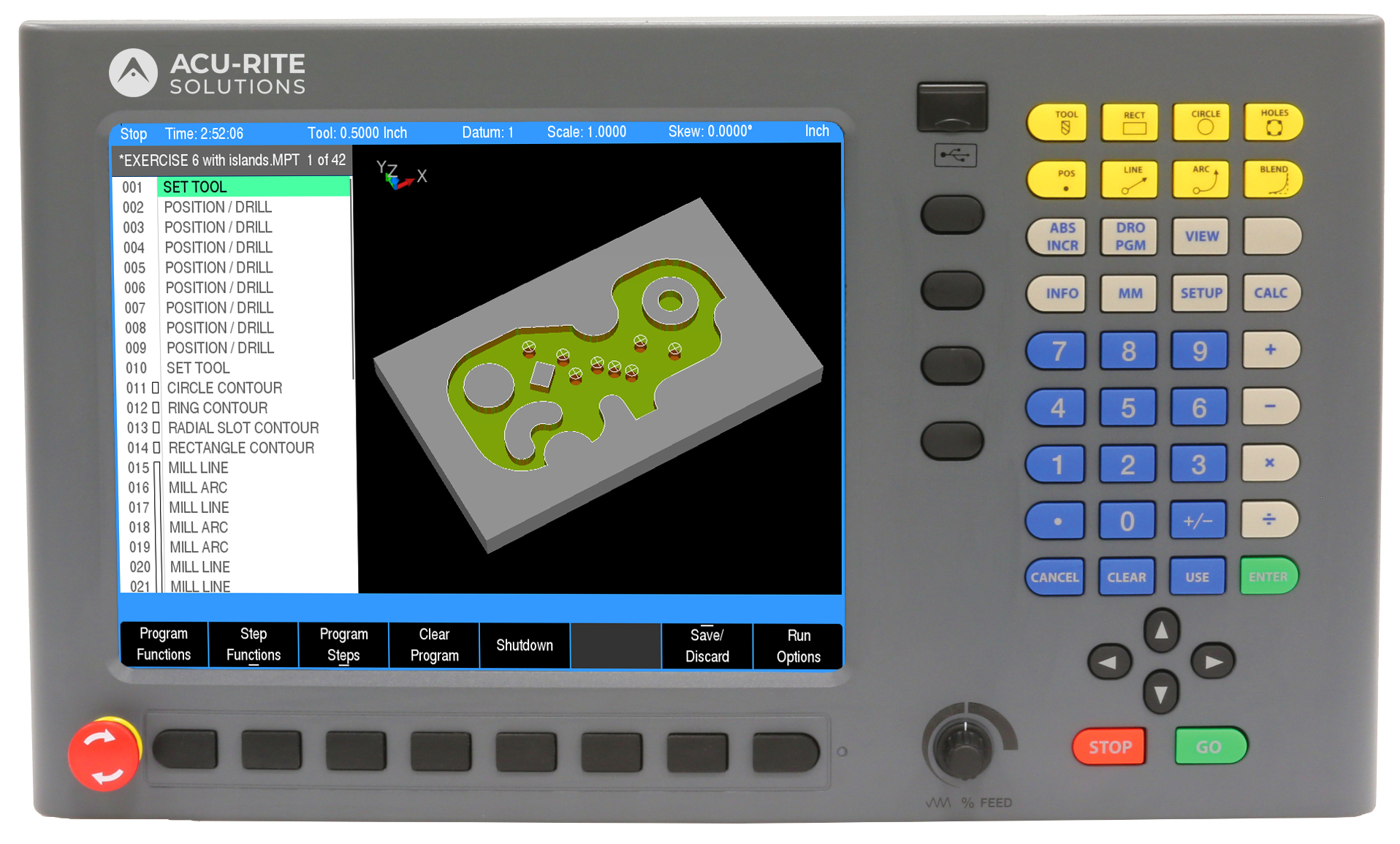
Stay Current on Precision Machining with Acu-Rite Solutions
Understanding precision machining trends is essential for machinists, manufacturers, and educators alike. From Bluetooth® integration and reshoring efforts to sustainability initiatives, education growth, and enhanced UX, 2025 offers opportunities to better prepare for the future of manufacturing.
Sign up for our monthly e-Newsletter at the bottom of this page to stay informed about precision machining and the latest news and product developments from Acu-Rite Solutions.