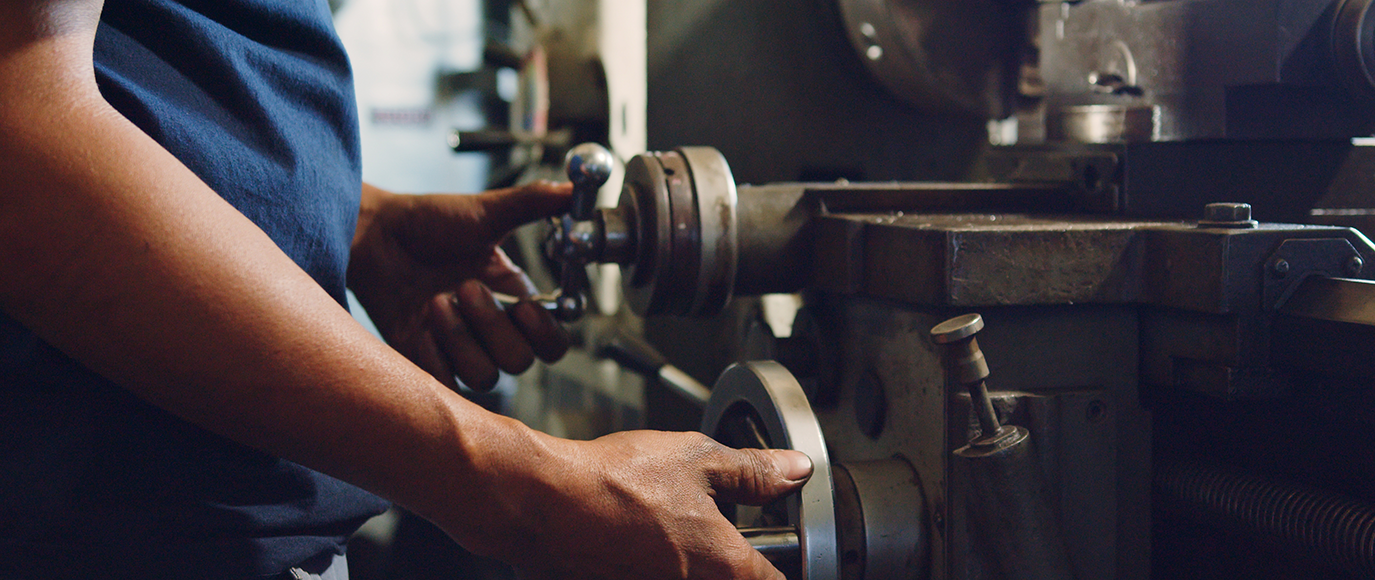
If you have any knee and bed mills sitting idle, taking up space in your shop, you’re not alone. It’s difficult to figure out what to do with a heavy manual machine or a run-down, outmoded CNC center. But “dealing with” idled machines doesn’t always mean having to get someone to take it or finding a way to get rid of it. Just because an old control is missing an impossible-to-find piece of hardware, or a machine is “just too difficult to do anything more with” doesn’t mean it can’t be a bigger revenue center.
There’s a strong chance you can get more value out of that good iron. The structures that underly machine tools haven’t changed much and stay sound long after the electronics of the original readout or control. Computer numerical controls (CNCs), on the other hand, have evolved dramatically since a lot the older machinery on today’s shop floors was built. That’s where we find the way to more life, more performance and more return from machines once thought scrap.
Controls have come to a point where manual knee and CNC-ready bed mills that were once thought too old and too new to justify a retrofit are more productive fits than ever. You can get almost all the advantages of a proprietary system, direct from the maker of your specific machine, and then some, without the extra cost. Here are 10 reasons to consider retrofitting knee or bed mill CNC controls:
1. Return on investment
First and foremost, extra machining capacity is acquired for significantly less than the cost of buying a new machine. In other words, you’ll definitely see return on investment with a retrofit before you will with a full machine replacement. Don’t let that good iron go to waste. Not to mention, a new machine requires significant downtime upfront for installation, reorganization of workflows, training, etc. Depending on the scale, retrofits often pay for themselves in the six months to two years.
2. User friendliness
It starts with large, color, high resolution screens that make life so much easier on operators. Modern CNC interfaces can also replicate existing CNC interface features and enhance them with improved graphics and custom screens, as on-screen graphics help smoothly guide users with conversational text. Programs can also be shown graphically, 2D or 3D, with edit capabilities right at the machine.
Seamless integration with hardware, like USB and CAD software make 3D work, transfer of data and offline programming simple. Controls’ PC-based interface is intuitive to modern operators, making them easy for training and developing teams, troubleshoot and/or prevent errors.
3. Reduced unplanned downtime
Modern CNCs have a much higher MTBF (mean time between failures) than older ones. Advanced system screens can provide clear graphics for faults and show solutions to resolve them. Plus, at this point, technicians know how to debug and troubleshoot modern CNCs faster than older controllers.
4. Storage capacity
Where legacy controls or DROs may not have even had storage, today’s CNCs have all kinds of virtual space for programs, tools and measurements. The latest MILLPWRG2, for example, has 2.5 GB of internal storage. Still not enough? No problem. USB and standard ethernet connections make memory effectively unlimited.
For some perspective, the original MILLPWR had 512 MB of storage.
5. Full-speed machining
Advanced contouring can cause older machines to slow down. That’s often because the CNC can only process and execute simultaneous movements so quickly. (There’s unused power in the machine.) Not only is this slower, but it can leave gouge or dwell marks on the part where a cutter lagged behind. That’s not an issue when the MILLPWRG2, for example, has a processor 1.4 GHz.
6. Interconnectivity and actionable data
CNCs have historically been isolated. Not anymore. Reconnecting a machine to a network with tooling or programming information can open up all kinds of possibilities. PC network protocols like Ethernet are so much faster than the previous serial communication, NC programs and data can be delivered to the control from a remote server in a fraction of the time. What’s more, some controls can send diagnostic data out, a huge advantage for maintenance planning and sourcing.
7. Error reduction
Modern controls allow for 3D modeling and simulations of parts directly at the machine. DXF files can be imported directly from a CAD file and saved. Users can simulate and find out if their part will be collision-free or not before pressing “start”. Controls also can have canned coding for common tool paths, processes and offsets that eliminate the need for typing in detailed sequences. Modern controls will even estimate how much machine time a part will take, giving operators the chance to adjust paths before it’s too late.
8. Easy installation and service
Every machine is a little different, wiring, dimensions, power sources etc. This certainly adds some challenges to fitting the right control. However, control makers, especially Acu-Rite Solutions, are eliminating a lot of the difficulties with custom engineered retrofit kits. We offer custom engineered kits for simple bolt-on installation for dozens of different machine brands. A retrofit kit, for example, can be built to include:
- Remote stop/go switch
- Ball screws
- Servo drives and motors
- Motor mounting castings and hardware
- Handwheels
- Precision linear encoders
- Console and encoder mounting hardware
- Machine-specific bracketry
- Recovery drive
What’s more, you can often upgrade and maintain the control inexpensively, with less vendor involvement, just like you would to an office PC. More proprietary or customized controls do not offer this flexibility.
9. Full G-code imports
CNC controls can make a very limited 3-axis machine into one that can handle advanced, multi-directional milling. The ability to import G-code unlocks all kinds of powerful functions and features. For one, spindle control that automatically adjusts spindle speed and/or direction on machines with an electronic variable speed spindle. Some controls have a “look ahead” feature that can detect sudden movements in the program and adjust. With code imported, controls also have built-in error compensation for linear and bidirectional non-linear movements.
10. Warranty coverage
Retrofit controls are often backed by strong warranty coverage. With our MILLPWR, receive a comprehensive two-year warranty that’s supported by a nationwide network of factory trained and certified distributors.
To learn more about what’s possible with a modern CNC retrofit, explore what our MILLPWRG2 control for manual knee and CNC-ready bed mills is capable of. Turn your idling machinery into value centers again.