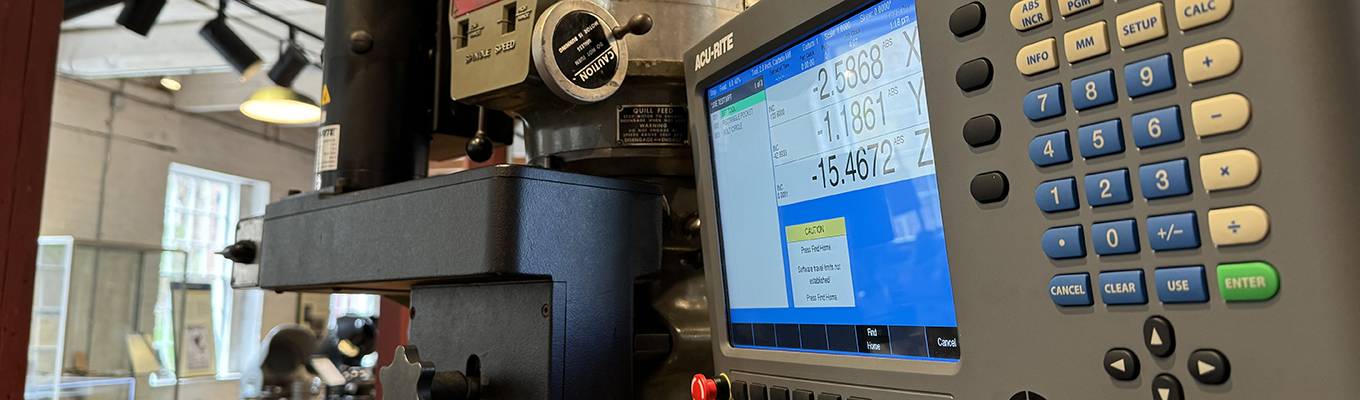
Nearly two centuries ago, the Robbins & Lawrence Armory in central Vermont sparked the development of precision manufacturing and machine tools in America. Today, it’s the home of the American Precision Museum (APM). Since 1966, APM has showcased American ingenuity by telling the manufacturing stories of yesterday, today, and the future.
The ACU-RITE MILLPWRG2 CNC control is vital to these efforts. Powered by the continuous innovation of HEIDENHAIN, the ACU-RITE control helps APM bridge the gap between traditional and modern machining methods. Together, we are engaging new audiences in the evolution of manufacturing—and inspiring the next generation of makers to continue the advancement.
The Birthplace of Modern Manufacturing
APM stands as a testament to the dawn of precision manufacturing. It is a historic site located in Windsor, Vermont, that played a pivotal role in manufacturing interchangeable parts in the 1840s, a revolutionary concept at the time. To create the interchangeable parts, the site repurposed existing machinery and built new equipment powered by water in the nearby stream.
These innovations enhanced the efficiency and quality of manufacturing, giving way to new standards that became the American system of Manufacturing. The American system led to consumerism, making everyday objects such as bicycles and typewriters more affordable and accessible to the masses.
APM preserves this rich manufacturing heritage by showcasing traditional machinery and artifacts as well as modern machine tools. Its signature 4,000-square-foot exhibit, Shaping America, illustrates how mechanized production drove industrialization and developed modern consumer culture.
Interactive Learning with the MILLPWRG2
The ACU-RITE MILLPWRG2 CNC control is more than just an exhibit piece at APM. It’s an educational tool demonstrating manufacturing machinery’s evolution to nearly 6,000 annual visitors.
HEIDENHAIN CORPORATION donated the MILLPWRG2 to APM in 2023, and it was installed on a 1960s Bridgeport mill in the museum’s Innovation Station. The MILLPWRG2 shows visitors in real time how CNC retrofit technology transforms manual machining methods.
“We learn so much from history, but some people won’t be drawn to the historical side,” Rex said. “That’s why we need modern technology to work with historical machinery. We need to show people how far we’ve come while encouraging them to help us reach the next level and bring us into the future of American manufacturing.
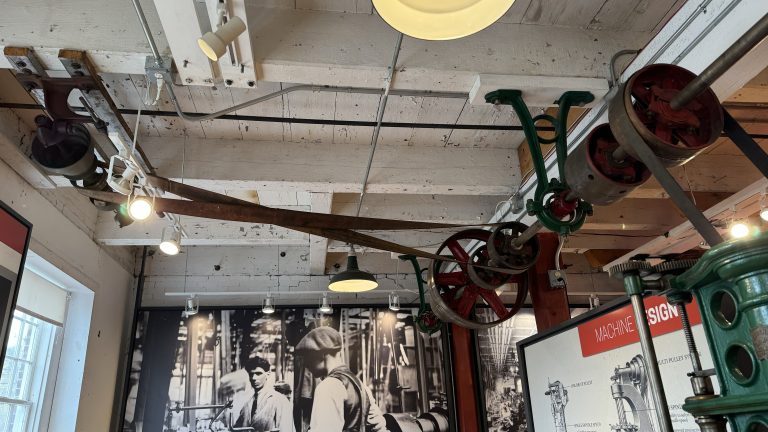
APM tailors demonstrations to the audience, which includes the public, students, and professionals from manufacturing companies. Generally, the goal is to show the Bridgeport mill’s original capabilities and its advanced precision and efficiency when retrofitted with the MILLPWRG2. The museum also uses the MILLPWRG2 to create items visitors can purchase in the gift shop.
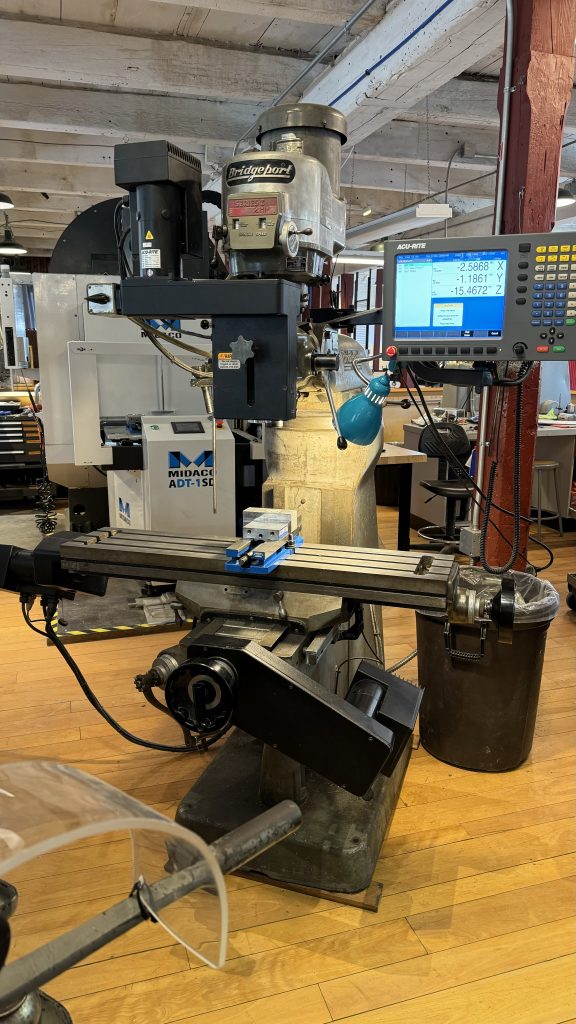
What Makes the MILLPWRG2 the Right Fit for APM?
The MILLPWRG2 is an entry-level CNC retrofit system that improves machining accuracy and efficiency, increasing the profitability of manual knee and bed mills with up to three axes.
The MILLPWRG2 is ideal for applications requiring both manual and automated machining, like APM. Other factors make it an excellent fit for APM, too. It has robust control capabilities yet intuitive operation, versatile retrofitting capabilities, and American-made durability. It also comes with comprehensive training and support.
Powerful Yet Intuitive
The MILLPWRG2 allows APM to use it as a full-function DRO system, a programmable CNC control, or both. Yet its intuitive design makes operation easy.
“Even on an older piece of equipment, you can do some pretty powerful things very simply by using a control like the MILLPWRG2,” Rex said.
The MILLPWRG2 has simplified navigation, ergonomic keyboards, conversational programming, and essential and advanced functions. Any machine tool operator can quickly learn how to use it, from machining students to experienced machinists.
Retrofitting Capabilities
When upgraded with the MILLPWRG2, existing mills gain a longer lifespan and advanced capabilities without a significant investment.
“We try to show people that every application doesn’t necessarily require a $200,000 or $500,000 machine. The ACU-RITE control on a Bridgeport can repeatably and accurately produce many parts that they need without taking a lot of floor space,” Rex said.
The MILLPWRG2 is compatible with 100+ machine makes and models, turning just about any legacy knee mill into a powerhouse. Many customers who purchased the first-generation model are still using it decades later.
Made in the USA
Like all ACU-RITE technologies, the MILLPWRG2 has been designed and built in the USA since day one. So, its application on a Bridgeport mill, a staple in American manufacturing, makes it a particularly meaningful addition to the museum.
“We are the American Precision Museum, so being able to use an American-made and supported product on another American-made product is a real benefit,” Rex said.
ACU-RITE products are crafted for lifetime durability. The MILLPWRG2 has rugged hardware and IP-rated seals, so it will stand up to even the harshest machine shop environments.
Dedicated Training and Support
ACU-RITE technologies are also supported in the USA for maximum reliability. Customers can access technical support by phone, appointment, or online in local time zones.
An ACU-RITE training specialist helped APM install and learn the MILLPWRG2. They ensured the museum staff and volunteers understood exactly how to operate the CNC mill controller so APM could effectively integrate it into its mission.
Customers who purchase from an ACU-RITE distribution partner also receive local support. Our distributors are factory-certified and authorized to support all ACU-RITE products in North America, including purchasing, delivery, installation, training, and service.
Inspiring the Next Generation of Manufacturers
MILLPWRG2 The high demand for manufacturing professionals is no secret. According to Manufacturing Institute and Deloitte research, 2.1 million manufacturing jobs are poised to go unfilled by 2030. There are plenty of job openings, but not enough people entering the profession to fill them.
APM is doing its part to address this gap through educational and career awareness programs. Its educational initiatives help spark interest in manufacturing careers by exposing students to the manufacturing technology and processes of the past, present, and future.
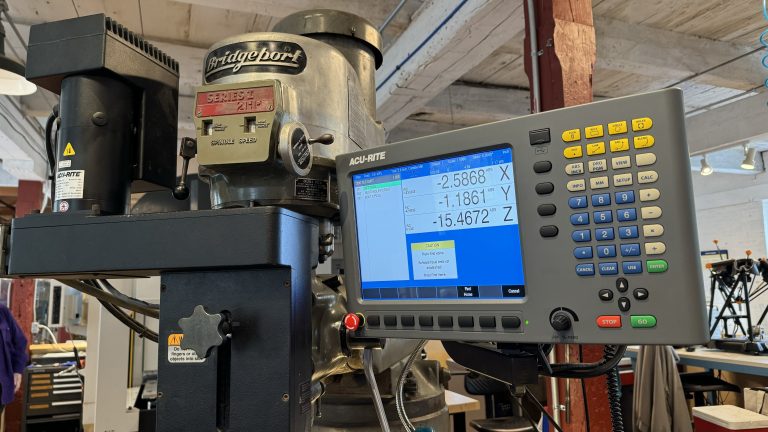
Each year, APM hosts field trips where students get to explore a variety of machining technologies. The MILLPWRG2 is central to these demonstrations.
“With the modern technology of the MILLPWRG2, we have digital readout capability, the ability to run programs, and conversational control that makes machining more interesting to the younger generation who are potential engineers and makers. Sometimes you’ll just see the sparkle in somebody’s eye,” Rex said.
APM also creates and distributes free STEM+M Kits (+M for Manufacturing) to fourth through sixth-grade students. They feature engaging challenges related to manufacturing, STEM, and design. Students may build a catapult, design tessellations, or construct a water wheel. Students can also explore APM in virtual tours.
Together, APM and HEIDENHAIN are providing education and inspiration to continue advancing manufacturing.
“HEIDENHAIN is committed to fostering the next generation of manufacturing professionals. We are proud to support the American Precision Museum for over a decade with U.S.-made and easy-to-use precision machining technologies,” said Gisbert Ledvon, Vice President of Marketing at HEIDENHAIN CORPORATION.
ACU-RITE’s School Discount Program provides technologies at a discount to North American schools with precision metalworking and vocational programs.
How to Upgrade Your Manual Mill with the MILLPWRG2
The MILLPWRG2 supports educators inspiring the next generation, professionals seeking higher production, and hobbyists pursuing their passions.
Explore the advantages of machining with the MILLPWRG2 and contact us for more information.