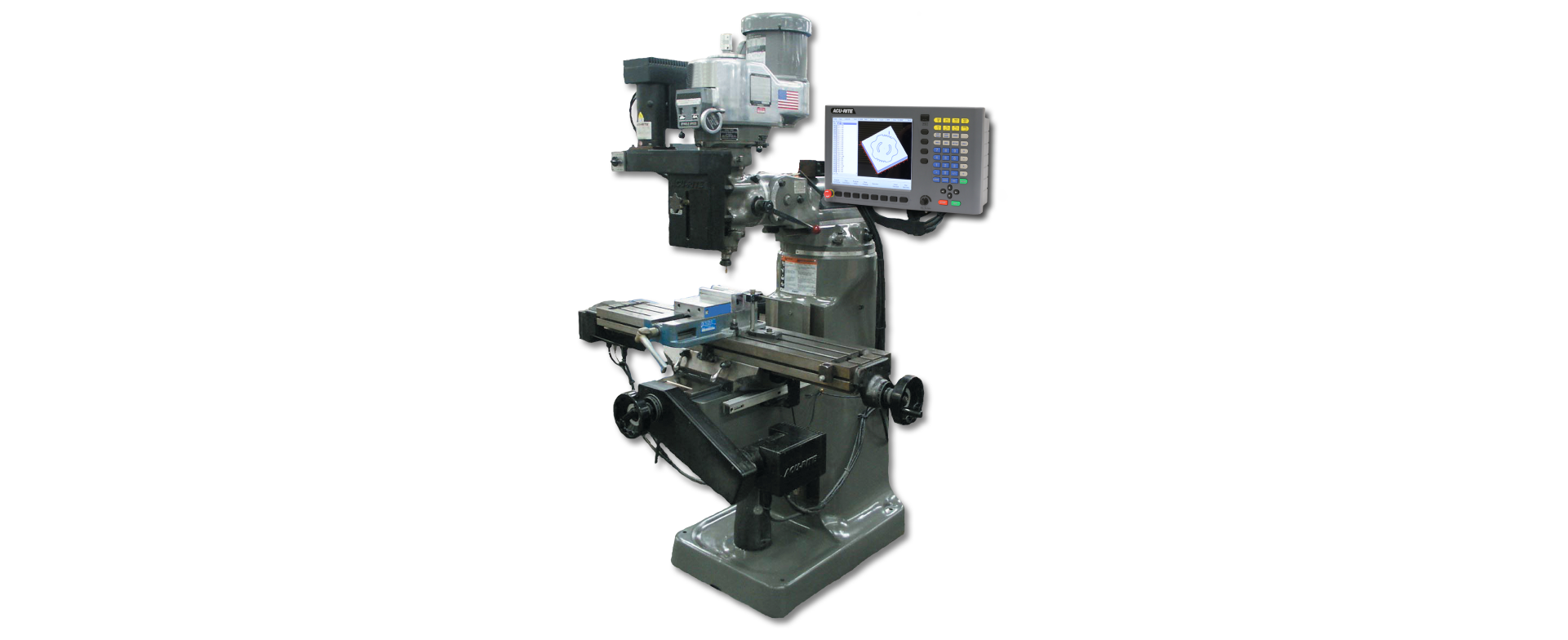
“I’m an engineer that likes to make things,” says Steven Emanuel, who holds a Master’s degree in Mechanical Engineering and is employed as a Laboratory Education Specialist in the University of North Carolina’s (UNC) Biomedical Engineering Department. “And with access to seven Acu-Rite Solutions MILLPWRs, I can do that every day.”
Emanuel explains that for seventeen years he has worked in a university setting, predominantly assisting engineering students bring their design projects to life in a fabrication laboratory. These projects are most often prototypes of biomedical devices and/or parts to support their ideas of something new to possibly assist mankind in the future.
“I am not a trained machinist myself, though I’ve learned by doing,” says Emanuel, who while working on his masters at the University of Michigan in (2005) was first given the opportunity to work in an engineering lab. There, Professor Robert Dennis mentored him while they supported students who needed to manufacture their engineering designs. “We had a MILLPWR control on a Bridgeport mill in the lab, along with a few other tools and were able to make all kinds of things. Right off the bat, I was able to grasp the conversational programming on the MILLPWR since it’s like having a discussion with someone. For example, if you were asked ‘where would you like your circular pocket on this piece of aluminum’ and you simply point out which coordinates. The MILLPWR basically does that then programs it and it gets done. This makes perfect sense to an engineering student. Now if you asked them to put in G-code, they’d be glassy-eyed and would need more training to do that.
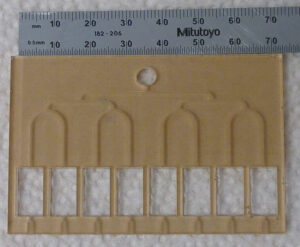
“From a teaching standpoint, it’s so powerful to be able to be productive so quickly,” adds Emanuel. “Not to sound cliché, but the MILLPWR control really is extremely intuitive. I can take an engineering student and in under an hour of pushing buttons, put them in a position to where they have a basic understanding of what the machine can do, including how to access and add certain features together to create a program for a part.
At the UNC biomedical engineering lab today where Emanuel now presides, the students are regularly exposed to CAD and overall fabrication. This can encompass milling using the MILLPWRs, 3D printing, laser cutting, as well as turning on a lathe, all with instructor oversight. Approximately 25 biomedical engineering students receive this experience at “The Shop” per term, though that number can vary. An example of one of the hundreds of projects overseen by Emanuel over the years includes a UNC biomedical graduate student’s research project. In this instance, she had designed a microfluidics that
fixture contained small tracks to allow her to measure the characteristics of small-scale fluid flow. Emanuel explains that each track channel was .020” across by .010” deep and her chosen material was acrylic. “We originally tried to develop this part with a laser cutter but that didn’t work very well, so we used some very small end mills, and by programming on the MILLPWR, she was able to successfully produce her design and make progress with her research.”
Emanuel adds that the support that he has received from Acu-Rite Solutions staff has also made a difference in helping him utilize all the features of the controls. “There have been multiple occasions where I have had to call in and they’ve been extremely helpful by guiding me to solve my problems at hand.”
Emanuel is also pleased to share that “The Shop” in his department currently has two MILLPWRs, as well two others in use at UNC’s Department of Public Health. And to support the love of machining on other projects offsite, he and Dr. Dennis have a personal lab with three other MILLPWRs. The latest addition purchased by Emanuel was through long-time Acu-Rite Solutions
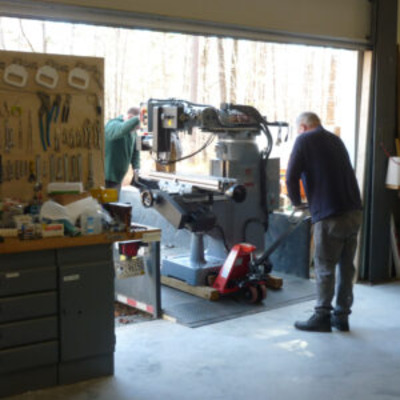
Machine delivery to offsite lab
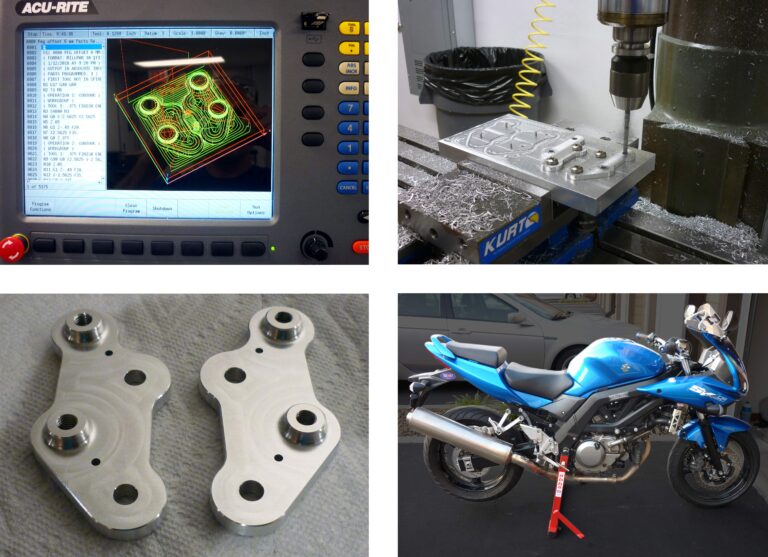
Custom motorcycle parts from start to finish: programming on the MILLPWR, machining them, finished parts, and installation.
distributor Scott Simister at OSS, LLC in 2021 who has supplied other MILLPWR machines to the University in the past. This most recent purchase was a MILLPWR integrated on an Acer mill and was delivered to the offsite lab.
At the offsite shop (see Steve’s Fab Lab), not only do Emanuel and Dr. Dennis work on private research projects but also personal projects as well. When Emanuel needed a custom part for his motorcycle, for example, he designed and produced it using the MILLPWR.
“The reason we keep getting MILLPWRs is because from Dr. Dennis’ first one at University of Michigan over 20 years ago, they’ve been reliable and very easy to use,” says Emanuel, “and subsequently very easy to teach on, so there has never been any reason to even consider anything else. And actually, I am now considering Acu-Rite Solutions latest TURNPWR control for lathes.”
Emanuel adds that one of the most complex machining projects on which he’s ever worked was with an engineering student who was part of the University of Michigan Formula SAE team where they design and develop racecars to participate in a worldwide competition. Here the project required some new parts including a portion of the rear suspension. “The rear uprights are rather complex parts, and they were completely programmed on the MILLPWR’s conversational system,” says Emanuel.
“Basically, what I really like about the MILLPWR is the fact that I can teach an engineering student some fundamental concepts of machining and conversational programming and they can very quickly be productive by making prototype parts and putting them to the test,” explains Emanuel. “And while it can’t do everything that a high-end control can do, it will do 95% of anything you need, and do it quickly, without requiring a lot of training. There’s a real elegance to having something so simple and commonsense that makes it extremely powerful.”
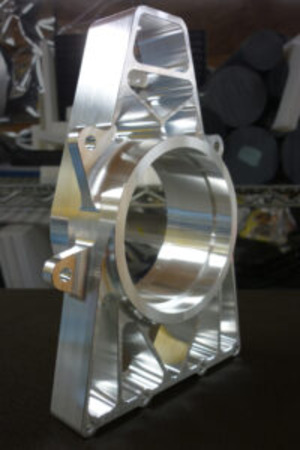
Custom racecar suspension part